Abstract
To analyze the impact of different hammer materials on the crushing effect of the impact crusher, the stereoscopic measurement of the Kleemann MR130 impact crusher and copper ore was carried out. The UG model of the Kleemann MR130 impact crusher was established and imported into EDEM software. The model of copper ore particles was established to analyze the crushing effect of impact crusher hammers material Cr26 and 35GrMo, taking the velocity and rotational kinetic energy of copper ore particles in 2.6~3.5 s as evaluation indexes. The simulation results show that when the feed rate is 15%, 25%, and 35%, the velocity and rotational kinetic energy of copper ore in the crusher with the hammer material of 35GrMo are higher than that of Cr26. Under the same hammer material, with the increase of copper ore feeding rate, the speed and rotational kinetic energy of the copper ore particle model are significantly increased; among these, the maximum speed of copper ore particle is 57.09 m/s, and the maximum rotational kinetic energy is 2269.39 J. The test results are consistent with the simulation results, which provide a research basis and a new idea for optimizing the impact crusher’s hammers and improving the copper ore’s crushing effect.
Impact crusher and granite model
Impact crusher model
Since the modeling ability of discrete element software EDEM is weak, and only the part in contact with it needs to be established in the simulation process of EDEM software, its three-dimensional model should be simplified. The three-dimensional model of the crusher is established in UG software, and its exterior and interior are shown in Figure 1 and Figure 2.
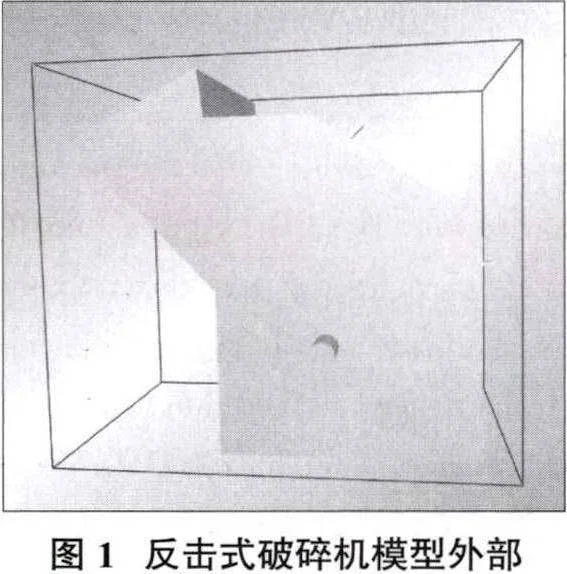
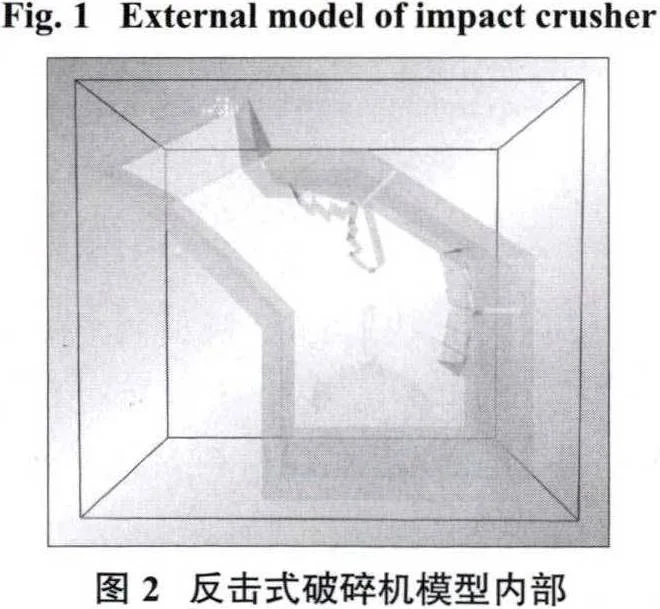
Research on impact crusher based on EDEM
The geometric size and shape of copper ore are random variables that directly affect its impact on the impact plate and the final crushing effect. This study focuses on the crushing effect of copper ore with the same geometric size and shape under different impact plate materials. Therefore, to accurately analyze the wear failure of the counter-plate in the crushed inner cavity, the copper ore (FIG. 3) was analyzed on the spot, and in combination with relevant literature and data, the copper ore was ordered to be spherical in discrete element simulation to facilitate simulation research. It is generated as a normal distribution with a mean radius of 185mm and a standard deviation of 0.191.
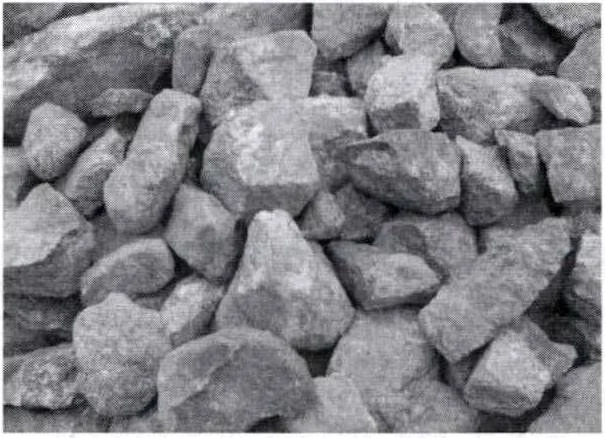
The density of copper ore is obtained by the density formula and drainage method. The experiment was repeated 60 times; the average result was 2.793g/cm³.
Software simulation
The contact model between copper ore, impact crusher, and copper ore is set as Hertz-Mindlin(no slip) build-in. The normal force between particles in this model is:
In the above formula, is the mean of the radius of all particles,
is the range of contact of particles and
is the mean of the elastic modulus of all particles, expressed as:
In the form above, form is the elastic modulus of one particle, and
form is the Poisson’s ratio of one particle. The
and
in the same expression.
Radial force can be expressed as:
In the above formula, δ is the area of overlap between interacting particles, and is the equivalent shear modulus calculated by the following formula:
In the form, G₁ and G₂ are the shear modulus of particles 1 and 2, respectively.
By importing the material library of the discrete element software and related literature in the early stage, the global parameters of the simulation with the impact crusher hammers material of Cr26 and 35GrMo (the rest of the crusher material is steel) are set as in Table 1.
Table 1:The global variable parameters of the impact crusher hammers materials Cr26 and 35GrMo | ||||||
Materials | Density/(kg/m³) | Poisson’s ratio | Shear modulus/Pa | Collision recovery factor (with copper ore) | Coefficient of static friction (with copper ore) | Coefficient of dynamic friction (with copper ore) |
Copper ore | 2790 | 0.2 | 3.0×10⁸ | 0.5 | 0.5 | 0.01 |
Steel | 7800 | 0.3 | 7.0×10¹⁰ | 0.5 | 0.9 | 0.05 |
Cr26 | 7980 | 0.27 | 7.5×10¹⁰ | 0.6 | 0.8 | 0.06 |
35GrMo | 2640 | 0.29 | 5.0×10⁷ | 0.2 | 0.5 | 0.01 |
The crusher model created in UG software was imported into EDEM software, and the particle plant was defined as being located inside the crusher. The rotor started to rotate in the inner chamber of the crusher at 3×10-⁶s. To show the working condition of the impact crusher, the particle plant is ordered to generate 400 copper ores (feed rate 25%) in the 2nd.5s inside the crusher, the rotor stops rotating in the 5ths, and the simulation is finished in the 6ths. Finally, the EDEM software is ordered to save the data every 0.1s for recording and outputting.
Figure 4 shows the impact force distribution of the impact plate when the simulation time is 3s. It can be seen that the impact force of the impact plate is mainly concentrated in the lower part of the impact plate, so it can be inferred that the lower part of the impact plate is the central part of the crushed ore. The possibility of wear failure in this part is greater, and the strength of this part should be optimized in the design.
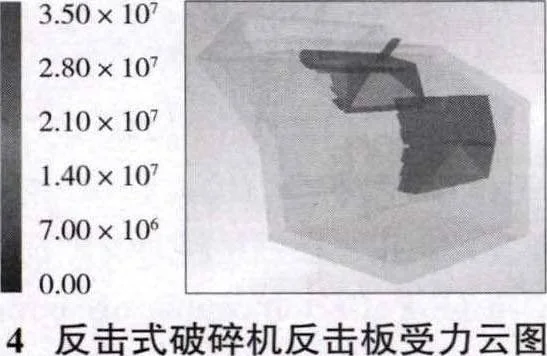
Simulation results of impact crusher
Comparison and research of simulation results
EDEM software defaults the particle as a rigid body in the simulation process, so it cannot simulate the process of particle breakage. However, the crushing of copper ore in the crusher is achieved by colliding with the hammer, the counter plate, and itself, so the crushing effect can be investigated indirectly by analyzing the speed and rotational kinetic energy of copper ore in the initial working period of the crusher. Using the EDEM data postprocessing module, copper ore’s velocity and rotational kinetic energy in different hammer materials were derived for periods of 2.6~3.5s. (Cr₂₆ and 35GrMo), as shown in Figure 5 and Figure 6. In Figures 5 and 6, Cr₂₆ and 35GrMo represented the hammer material of Cr₂₆ and 35GrMo.
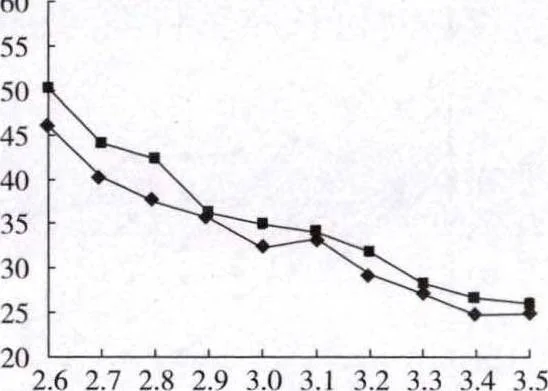
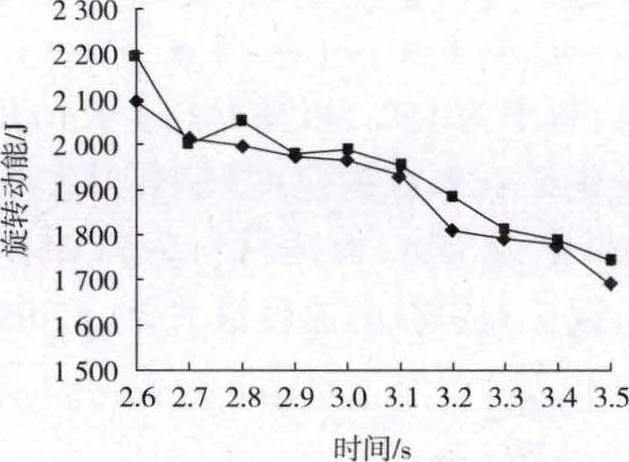
As shown in Figure 5, when the hammer material was Cr₂₆ and 35GrMo at the time points of 2.9s, 3.1s, and 3.3s, the velocity of the copper ore was relatively close. At other time points, the velocity of copper ore appeared to be larger than that of Cr₂₆ when the hammer material was 35GrMo. That is, changing the hammer material could change the impact velocity of copper ore.
As shown in Figure 6, when the hammer material was Cr₂₆ and 35GrMo at 2.7s, 2.9s, and 3.4s time points, the rotational kinetic energy of the copper ore was relatively close. At other time points, the rotational kinetic energy of copper ore was larger than that of Cr₂₆ when the hammer material was 35GrMo. That is, changing the hammer material changed the rotational kinetic energy received by the copper ore. Therefore, through the study of plate hammer material by discrete element method, it was found that the crusher hammer material was 35GrMo. At the initial working stage of the crusher, its crushing velocity and rotational kinetic energy were higher than that of the hammer material as Cr26.
Simulation experiment verification of different feed rates
According to the simulation steps, all parameters remain unchanged except the feed rate of the crusher. When the hammer material was Cr₂₆ and 35GrMo, and the feed rate was 15%, 25%, and 35%, respectively, copper ore’s velocity and rotational kinetic energy were analyzed. The results are shown in Fig.7 and Fig.8. A(15%) represented copper ore’s velocity and rotational energy when the hammer material was Cr₂₆, and the feed rate was 15%. B(15%) represented copper ore’s velocity and rotational energy. When the hammer material was 35GrMo, the feed rate was 15%, and the rest were the same.
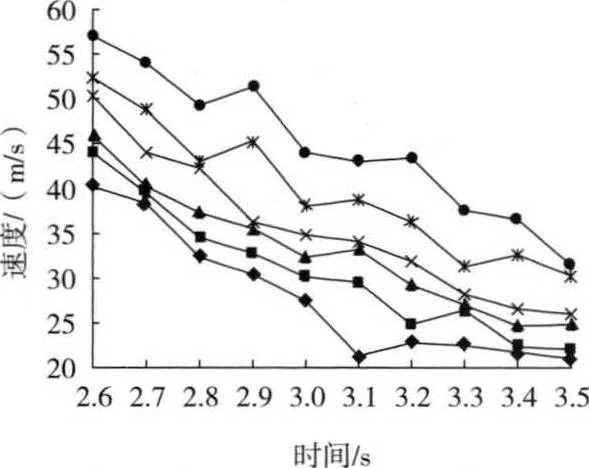
◆—A(15%); ■—B(15%): ▲—A(25%);
×—B(25%);*—A(35%); ●—B(35%)

◆—A(15%); ■—B(15%); ▲—A(25%);
×—B(25%);*—A(35%); ●—B(35%)
As seen from Figure 7, when the feed rate of copper ore is 15%, 25%, or 35%, the speed of copper ore in the crusher is different. When the feed rate of copper ore was the same, so was the speed of copper ore. When the hammer material was 35GrMo, it was higher than that of the hammer material, which was Cr26. When the impact crusher hammer material is the same, the copper ore’s speed increases obviously with the increase of the crusher’s feed rate. When the feed rate of copper ore was 15%, and the plate weight material was Cr26 with a time of 3.5s, the particle velocity of copper ore was the smallest, being 20.97m/s. When the feed rate of copper ore is 35%, the hammer material is 35GrMo, and the time is 2.6s, the speed of copper ore particles is the highest, which is 57.09m/s.
When the feed rate of copper ore was 15%, and the plate weight material was Cr26 with a time of 3.5s, the particle velocity of copper ore was the smallest, being 20.97m/s. When the feed rate of copper ore is 35%, the hammer material is 35GrMo, and the time is 2.6s, the speed of copper ore particles is the highest, which is 57.09m/s.
As shown in Figure 8, when the feed rate of copper ore is 15%, 25%, and 35%, the rotational kinetic energy of copper ore is different. When the copper ore feed rate was the same, the rotational kinetic energy of the copper ore in the crusher when the hammer material was 35GrMo was significantly higher than that of the hammer material Cr26. When the plate hammer material is the same, the rotational kinetic energy of the copper ore in the crusher increases obviously with the increase of the copper ore feed rate. When the feed rate of copper ore was 15%, and the hammer material was Cr26, the rotational kinetic energy of copper ore was the smallest, which was 1627.31J. When the feed rate of copper ore was 35%, and the hammer material was ZG35GrMo, the rotational kinetic energy of copper ore was the largest, 2269.39J.
Test verification
Apply the laser particle size analyzer (Figure 9) to analyze the copper ore crushed with different hammer materials and different feed rates, take the single particle size less than 15mm as the standard, weigh out the weight of the extracted copper ore particles and the weight of the copper ore particles with the size less than 15mm, and use the ratio δ (Eq. (5)) of the two to evaluate the crushing effect of the good or bad.
Where M is the weight of extracted copper ore particles; m is the laser particle size analyzer used to detect the weight of copper ore particles that meet the standard.
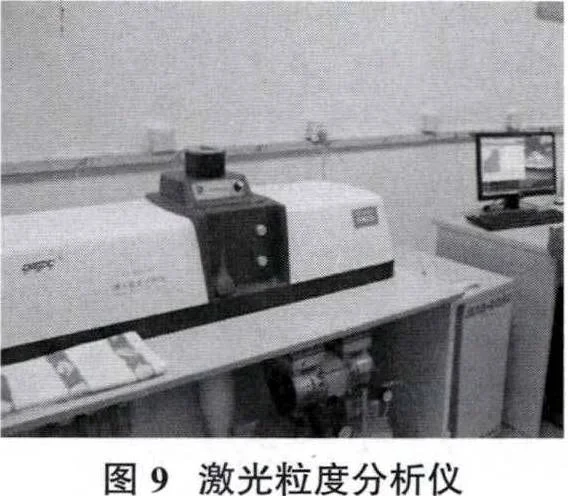
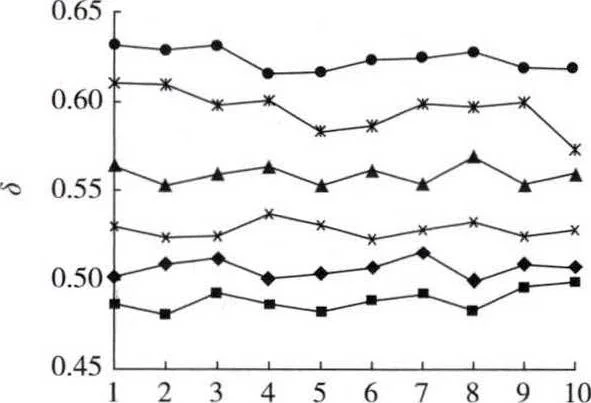
◆—A(15%): ■—B(15%): ▲—A(25%);
×—B(25%);*—A(35%); ●—B(35%)
The crushing effect of the impact crusher with different hammer materials and feed rate simultaneously is calculated, and the results are shown in Figure 10.
As shown in Figure 10, when the feed rate is 15%, 25%, 35%, and ten repeated tests, the crushing effect of the hammer material ZG35GrMo is better than that of the hammer material Cr26. In the same hammer material in the same crusher, with ten repeated tests, the best crushing effect appeared at the feed rate of 35%, and the worst crushing effect appeared at the feed rate of 15%. The crusher appeared with the increase in feed rate, and the crushing effect of copper ore increased. The results are consistent with the simulation results.
Conclusion and prospect
- The velocity and rotational kinetic energy of copper ore in the crusher when the hammer material was 35GrMo was significantly higher than when the hammer material was Cr26. In other words, the crushing effect of copper ore was better when the hammer material was 35GrMo than when the hammer material was Cr26.
- Change the feeding rate of copper ore for simulation verification: in the same crusher and the same material of hammer, with the increase of feeding rate, the speed and rotational kinetic energy of copper ore gradually increase; that is, the impact of copper ore is more and more intense, the better the crushing effect. Among them, the maximum value of copper ore’s speed and rotational kinetic energy appeared in the feeding rate of 35%, the hammer material is 35GrMo, and its value is 57.09m/s and 2269.39J.
- The effect of hammer material and feed rate on the crushing effect is obtained by comparing simulation and test results, and the simulation results are verified. The results provide a theoretical basis for optimizing the impact crusher’s hammers and improving the copper ore’s crushing effect.